🧪 Test Subject: Adidas’ 3D-Printed Slip-On
Future Feet, Assemble!
By Defiant Labs | Broadcast from Sector 3D-42X
Somewhere in the neon-lit future of footwear, Adidas has cracked open the vault and unleashed a sleek, slip-on sneaker straight out of a cyberpunk fever dream. And guess what? They 3D printed it.
In a bold stride toward high-tech fashion, Adidas just dropped a 3D-printed marvel known as the 3D CMPT, short for “3D Compression.” It’s part sneaker, part sculpture, and all sci-fi swagger. This isn’t just another running shoe — it’s a minimalist latticework of innovation that looks like it was printed inside a moon base and smuggled back to Earth through a temporal rift.
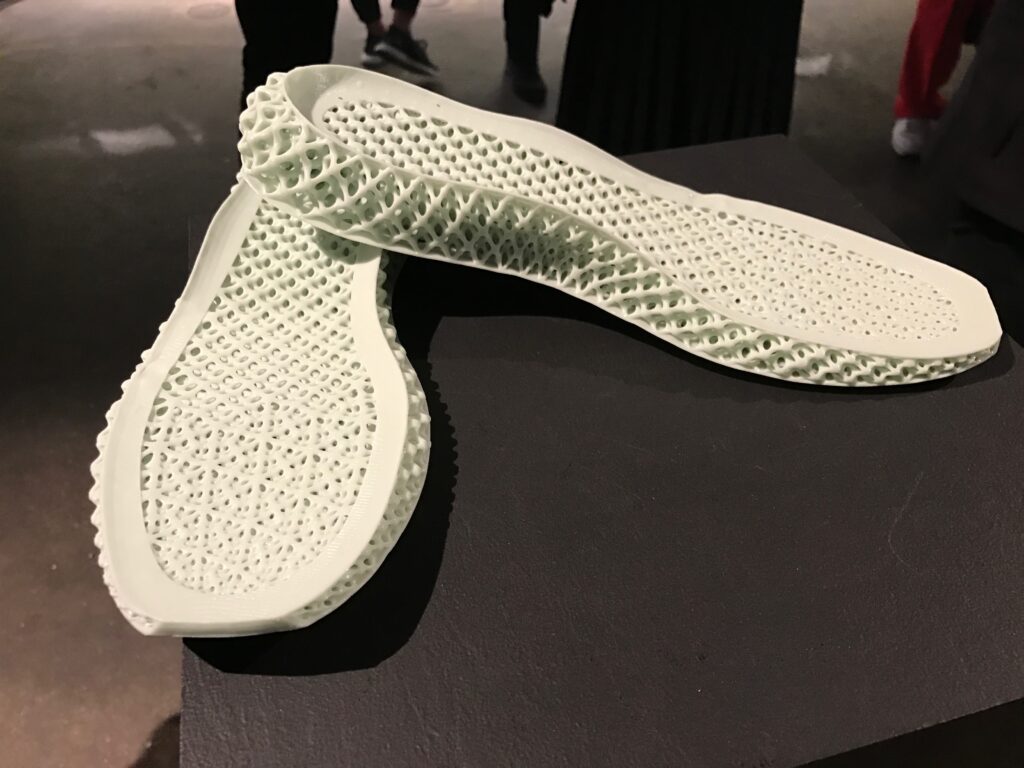
🧬 The Science Behind the Shoe
The 3D CMPT is created using a digital lattice structure fabricated through Carbon’s Digital Light Synthesis™ (DLS) — a process that uses light and oxygen to grow parts from a pool of resin. In other words, this shoe wasn’t stitched or sewn… it was summoned. From the void. With lasers.
DLS allows Adidas to generate intricate, high-performance midsole structures that can’t be made by traditional methods. The result? A shoe that’s light, breathable, and looks like it’s one firmware update away from gaining sentience.
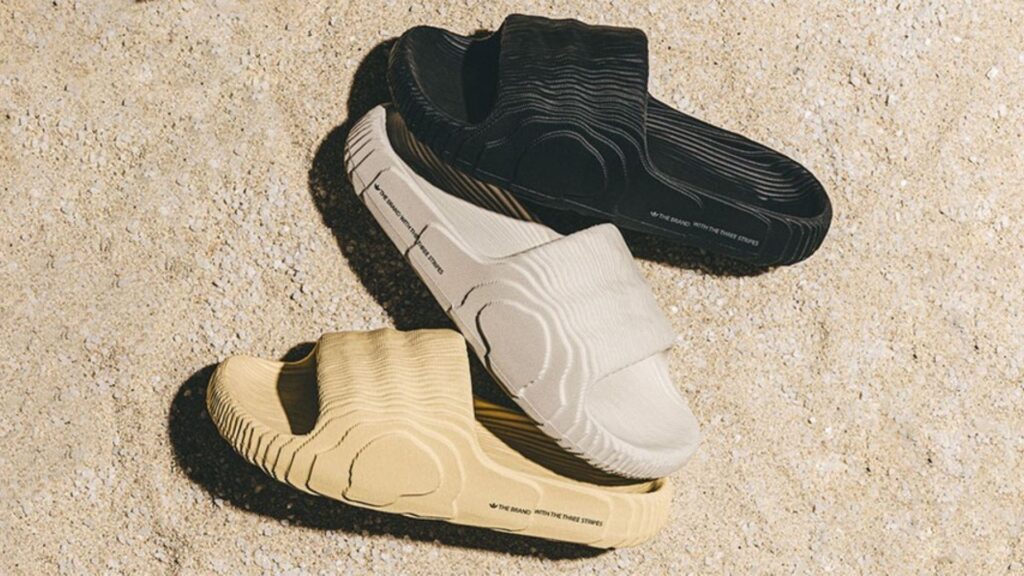
🧢 Fashion or Function? Trick Question.
The design is slip-on — no laces, no gimmicks. Just pure performance polymer. The outer shell is a flexible web of interconnected hexagonal cells that conform to your foot while still maintaining structural integrity. Think of it like walking on the exoskeleton of a nanobot.
Even more impressive: it’s sustainable. Adidas has long been in the game of eco-conscious design, and the 3D CMPT continues that tradition. Less waste. Fewer materials. More control.
And in classic Adidas style, it’s all tied together with a sleek monochrome look. It’s like the shoe version of a stealth drone — smooth, silent, and kind of intimidating in the best way.
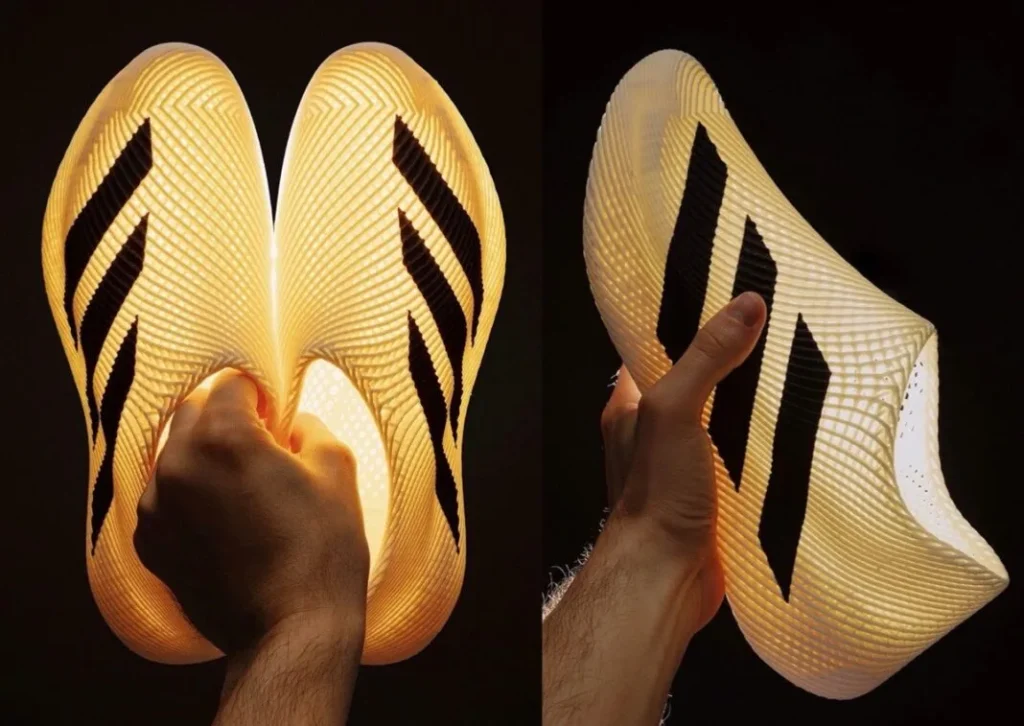
🧠 Why This Matters to Makers
If you’re a 3D printing nerd (and let’s face it, if you’re reading this, you probably are), this drop signals a major shift. Big brands are finally leaning into additive manufacturing not just for prototyping — but for consumer-ready, performance-grade products. That means the skills you’re honing in your garage lab? They’re the future of production.
The lattice structures. The on-demand fabrication. The software-to-object pipeline. Adidas is laying down the blueprint for the factory of tomorrow — and if you’re clever enough, there’s room at the design table.
Just don’t sit in Dr. Defiant’s chair.
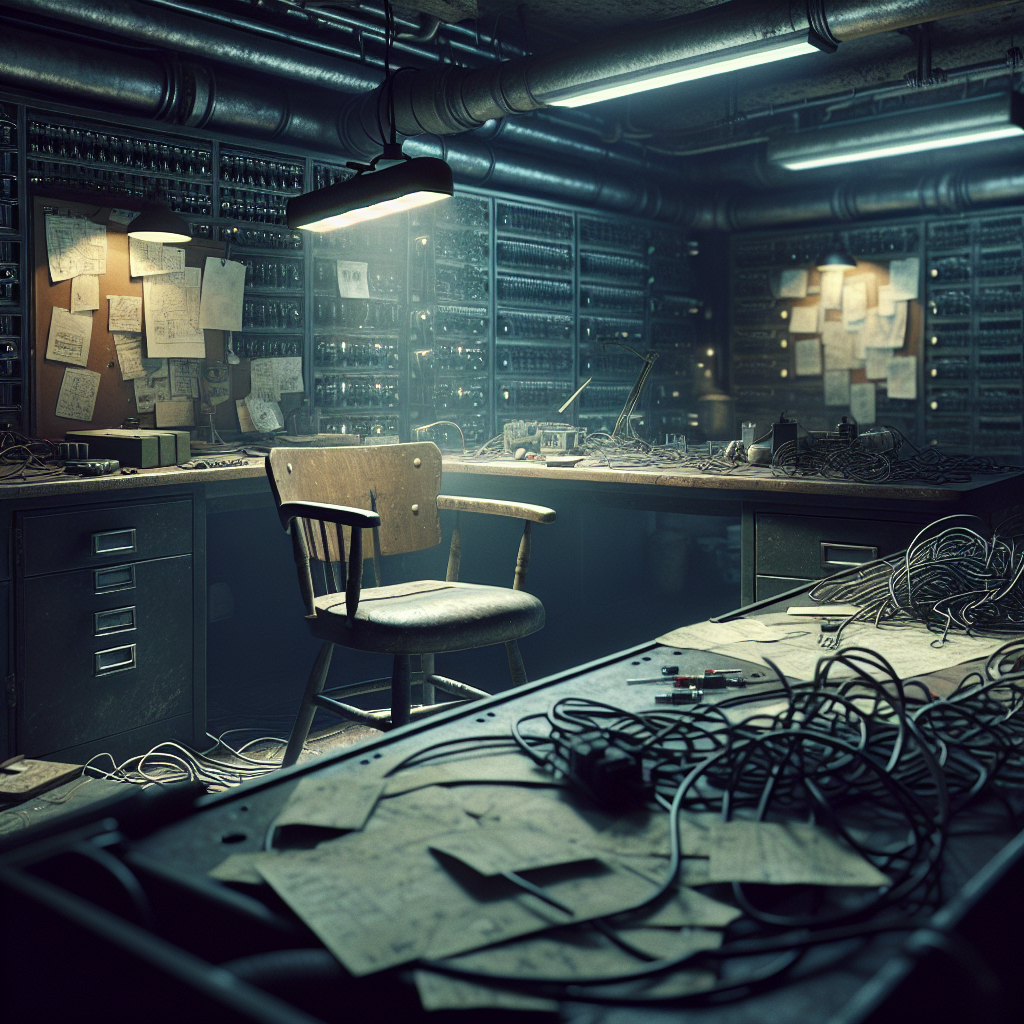
⚡ Lab Notes
- No glue, no sewing – The shoe is printed as one cohesive structure.
- Limited release – Only available in select regions and for short durations.
- Real-world performance – Great for light training and athleisure, not ultramarathons.
- Potential applications – Orthotics, wearable tech, modular gear, and custom footwear.
🛠️ What’s Next?
We’ll be watching this closely from the bunker. Because if Adidas can print a shoe like this today, imagine what’s coming next…
- Exosuit boots?
- Reactive tread soles?
- Biomechanical insoles that track your steps and your secrets?
We’re ready. Printer armed. Laces… irrelevant.